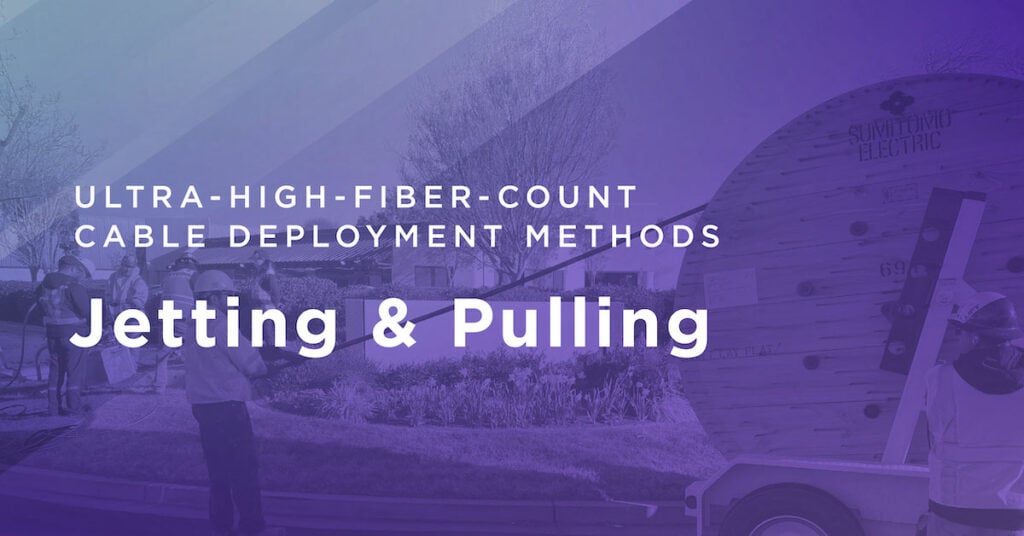
The pace of construction for large-scale data centers (DCs) is rapidly increasing worldwide. As networks process more and more data, they require quick increases in transmission capacity. One issue arising from the increase in demand is that the cables that connect DCs are installed in underground ducts with limited space and with short installation timelines. Despite these challenges, DCs are mandated to maintain contracted Service Level Agreements (SLAs). This dilemma has resulted in a demand for optical fiber cables with higher density which maximize duct space and minimize installation time and cost.
In response, Sumitomo Electric Lightwave (SEL) has developed Ultra-High-Fiber-Count (UHFC) cables, high-density cables with drastically reduced cable ODs. This reduction creates massive data capacity while maximizing limited duct space, which allows for a 6,912f-count cable to easily fit into a 1.5” duct.
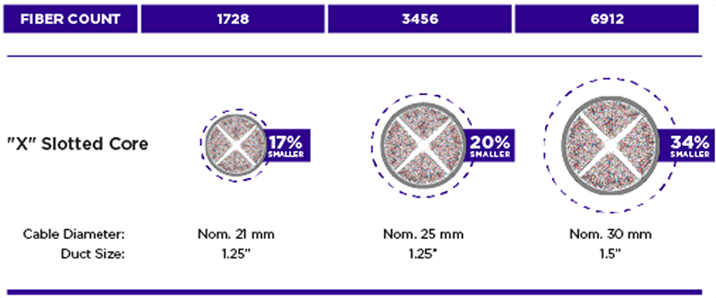
With fiber density, cable size, and durability in place, the only question remaining is how best to deploy UHFC cables. A quick look at the fundamentals of pulling technology vs. jetting technology highlights key differences, including installation time, deployment cost, cable damage risk, and the continuous cable lengths that can be achieved during deployment.
Pulling Installation
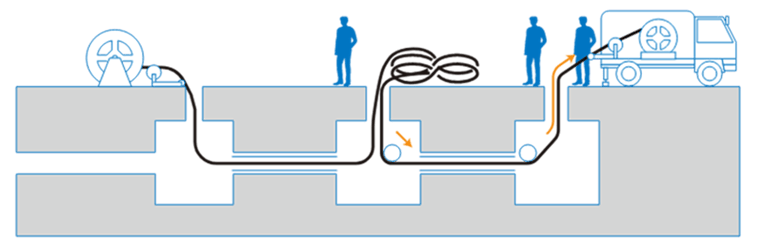
Cable pulling, pre-terminated or not, is considered the industry standard. . This method involves pulling a fiber optic cable through pre-installed underground or aerial ducts. While this allows you to choose between manually pulling the cable or using a reeling machine to assist, it is often completed with machine assistance, particularly when deploying over longer OSP distances. Both manual and machine-assisted pulling require frequent “intermediate assist points” at which cables are pulled through the duct, placed into handholds or access points, and spliced together, often necessitating “figure-eight” looping to prevent cable twisting when the duct changes direction. This process requires additional workers and equipment movement from location to location resulting in additional deployment costs and time at an average pull rate of 50 feet per minute.
Jetting Installation

Jetted technology, pre-terminated or not, is considered the less disruptive option thanks to its minimal touch points throughout the deployment This method is achieved by jetting a cable through an underground duct (aerial ducts can be used for short distances) using compressed air while simultaneously pushing the cable into the duct. This is only possible with the use of machinery. Considerably faster than pulling cable, jetting cables move at 150 feet per minute or higher speeds. Jetting allows for a smooth transition through duct turns and curves by reducing friction and placing less strain on the cable, allowing for deployment lengths into the thousands of feet. This eliminates many, if not all, “intermediate assist points” and associated labor. As expected, less labor, faster deployment times, and fewer materials lead to an overall reduction in deployment cost.
To prove jetting technology’s effectiveness and cost savings, SEL has partnered with Lightwave Construction, a turnkey fiber installation, termination, testing, and maintenance solutions provider, to deploy a variety of cables in the U.S. Using jetting technology, they installed 432f-count microduct cable at an average deployment speed of 30,000 feet in a 4- to 6-hour window with limited disruption to the community. This contrasts with the traditional pull method, which only reached 20,000 feet in 18 hours. Based on this successful test, Lightwave Construction and SEL recently used jetting technology to deploy a 6912f-count OSP cable in an urban area, easily achieving 10,000 feet within a day. In contrast, the pulling technique only allows for 3,000 feet when conducted in the same timeframe. Both successful tests demonstrate that jetting maximizes duct space and minimizes installation time and cost when compared to the pulling method.
Tag(s):